Limitless communication
The complexity of industrial automation tasks is continually increasing, leading to the development of more and more distributed control concepts. These approaches allow for more individual, flexible and modularly structured automation technology as intelligent peripheral devices connected over industrial Ethernet become increasingly prevalent. It is becoming more common, for example, for individual machine parts or components to be equipped with their own controllers and grouped together to make up a completed machine.
Trouble-free communication
Effective communication between individual subsystems and components is of crucial importance for the productivity of these types of solutions. In the early days of industrial electronics, systems communicated using individually programmed interfaces or device drivers. Nearly two decades ago, the automation industry began searching for ways to provide interoperability without requiring application programming.
One such approach is OLE (Object Linking and Embedding), a data exchange protocol developed by Microsoft in 1992 for office applications that resides directly in the operating system. OLE allows things like integrating values from external data sources into tables or incorporating tables and images into documents. Standardized software interfaces for exchanging data between applications from different manufacturers were then developed based on this protocol and introduced in 1996 under the name OPC (OLE for Process Control). Since 1998, they have also been included in Automation Runtime, the real-time operating system from B&R.
One system for different manufacturers
Manufacturers of end devices used in industrial automation can set up an OPC server to take advantage of data from OPC clients in controllers, SCADA systems and HMI devices. OPC is very simple to use, as evidenced by the drivers delivered along with office printers that made it possible for the printer to be integrated into the entire Windows office environment. "This has considerably reduced the amount of effort required to program communication tasks," says Hans Egermeier, business manager of automation software at B&R. "More important, however, is that it made it cost-effective to develop distributed systems with software and devices from different manufacturers in the form we are accustomed to seeing today."
Software development for OPC-compliant products relies on another technology from Microsoft for a common framework: COM/DCOM (Distributed Component Object Model). On one hand, this offers the advantage of a technological platform with a high degree of stability due to its wide distribution. On the other hand, developers have to face the limitations of DCOM, for example time consuming configuration without the possibility to set parameters for timeouts or high availability. Important points of criticism include being tied to the Windows operating system and a lack of control due to the proprietary nature of COM/DCOM. In addition, an OPC server must be set up on separate Windows-compatible PC hardware in order to implement a system with OPC communication.
Any platform
Overcoming all of these shortcomings is the goal of OPC UA (Unified Architecture), the specification of which was completed in 2009 by the OPC Foundation. This technology combines the previously separate specifications for data, events, objects or commands into a single unified standard. OPC UA also has a service-oriented architecture (SOA) with various communication layers and a separate communication stack as a replacement for the previously used COM/DCOM technology. This simplifies porting to various technologies and allows safe, reliable, and platform-independent transport of raw data as well as preprocessed information from sources ranging from field devices to production planning or ERP systems.
Available in ANSI C, C# and Java, the OPC UA communication stack can be ported to any operating system or embedded hardware and compiled for use in multi-thread or single-task operations. This allows any intelligent end device to act as an OPC UA server regardless of manufacturer, programming language and operating system while making an intermediary PC unnecessary.
"OPC UA provides complete scalability – from embedded control software to management information systems," explains Egermeier. Not only does the OPC UA communication standard offer a separate role-based authentication system based on today's standards, it also supports certified safe connections and completely transparent configuration all the way down to the timeout for each service operation. It also makes it possible to slice large data packets to make them manageable for smaller systems through chunking.
Dr. Hans Egermeier |
![]() | ![]() |
OPC UA allows direct communication between different applications on any hardware and operating system platforms. | OPC UA uses basic services and the OPC information model to define how data is accessed. |
The Automation Studio development environment supports OPC UA and makes it easier to connect B&R automation solutions to all types of HMI clients, SCADA packages and smart devices. This allows application engineers to concentrate on their actual automation tasks so they can produce better systems to the market more quickly and efficiently. |
Investment security with OPC UA
In OPC UA, all authorized applications on a client are supplied the required information from any servers in real-time in the form of data types, CPU variables with properties, methods or tasks – and this is done independent of fieldbus or other transfer mechanisms used. The standard uses basic services and information models to define the way data is exchanged between conventional TCP/IP transport mechanisms and the data models defined by device manufacturers and standardization organizations such as PLCopen. The same applies across different networks and across different companies via the Internet and through firewalls.
"The browsing function in OPC UA makes it easier to set up industrial communication between devices from different manufacturers. With this function, clients automatically determine which servers are available and what type of data each of them can provide," says Egermeier. The use of a metamodel makes it possible to evaluate the data types and semantics of the information. This contributes substantially to making the system future-proof since it eliminates the need for an application or operating system to be designed to handle all future server device possibilities from the very beginning.
![]() |
With client-server architectures, OPC UA provides uniform, manufacturer-independent mechanisms for data and program access throughout all levels of industrial automation. |
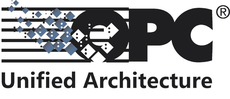
Implementing application complexity as needed
The OPC UA communication protocol will no doubt become an established standard for plant networking within a short period of time, owing greatly to its openness and ease of use. "Beginning with a standardized, simple default view simplifies configuration of applications with limited complexity," says Egermeier. "If necessary, configurations can be easily adapted to the respective level of complexity using requirements-oriented user views without running up against any limitations."
The Automation Studio development environment supports OPC UA data access and makes it easier to connect B&R automation solutions to all types of HMI clients, SCADA packages and smart devices. This allows application engineers to concentrate on their actual automation tasks so they can introduce better systems to the market more quickly and efficiently.
Whether from the simple default view or individual user views, any level of complexity can be represented through simple configuration steps. |